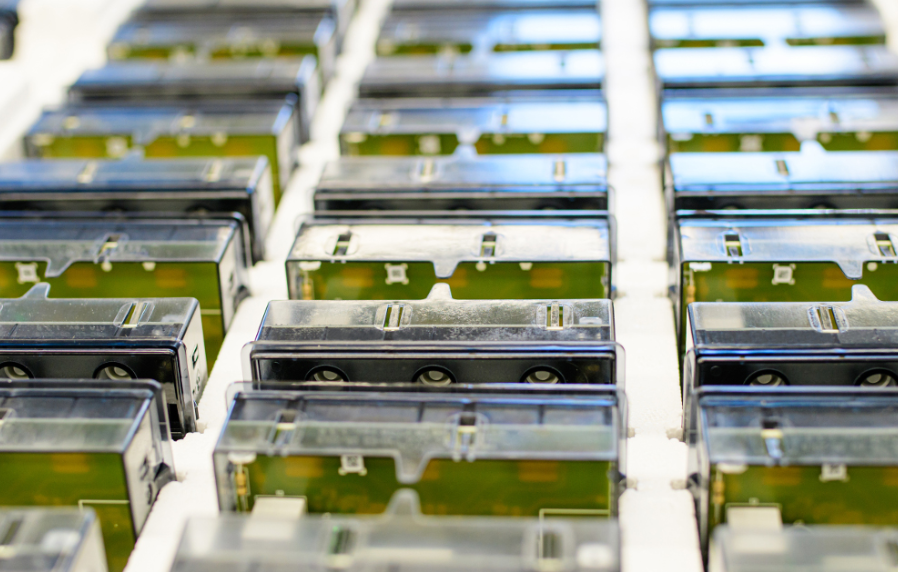
Manufacturing electronics in an external EMS company provides additional opportunities to increase production efficiency and reduce costs
Why manufacturing electronics in an external company?
How to reduce the production costs so as not to lose out on product quality?
How big a role does price play in choosing an EMS partner?
Which way of working with a contract manufacturer can maximise the benefits?
Manufacturing electronics in an external company is a strategic decision that is always driven by a number of factors. The most common are cost optimisation, the benefits of economies of scale, the reduction of time to market of the final product and gaining a high degree of flexibility in the area of production costs. Of course, once the terms of cooperation with a partner have been agreed, cost reduction is subject to cyclical negotiations. How can price reductions be achieved if neither the chosen materials nor the production process have changed?
Nowadays, it is rare to attempt to lower quality requirements in order to reduce unit costs. The times when unit cost was the most important indicator are irrevocably gone, because final customers no longer expect just a product that is attractively priced, but also one that provides adequate durability. Sustainable production methods and an appropriate image for those involved in the supply chain are also increasingly important. In an age of rapid information exchange, if a product does not meet the quality requirements, the customer will very quickly become discouraged about the brand and, through their opinions, dissuade potential customers from buying. Therefore, an illusory saving in the form of a reduction in unit cost can be counterproductive, causing a long-term decline in revenue and brand value.
Electronics manufacturing is a complex and sophisticated process consisting of design, BOM completion, assembly and quality control and testing. Potential optimisation opportunities apply to each of these stages.
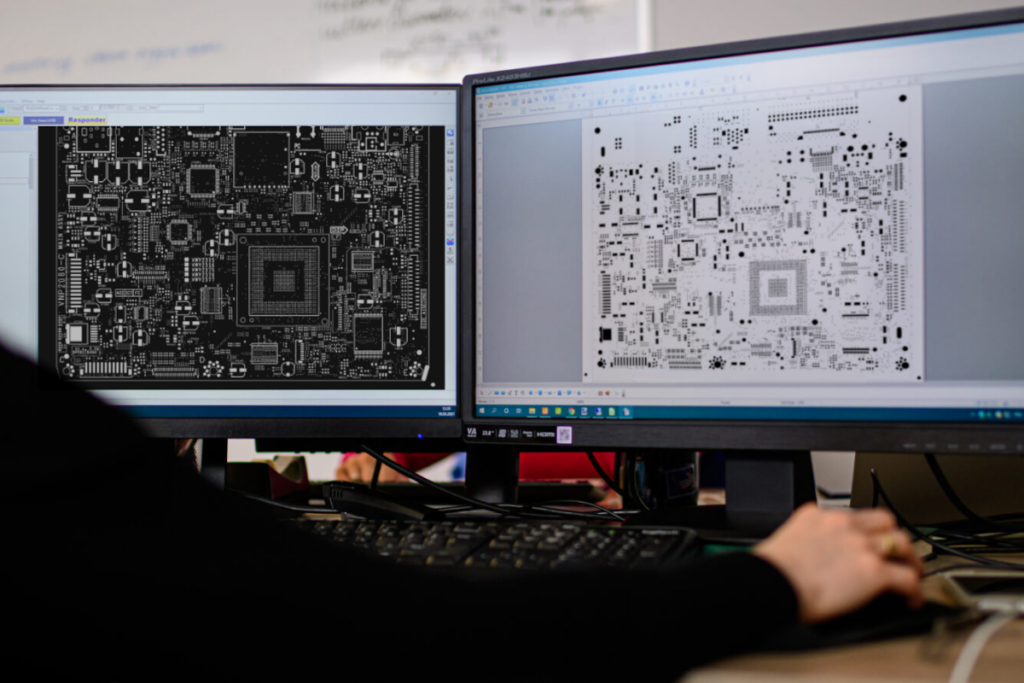
Collaboration between the OEM’s engineers and those of the contract manufacturing service (EMS) partner can bring tangible benefits. There are often instances where a minor design change can yield significant savings. For example, adjusting the placement of individual components can allow for:
- reducing the number of processes – e.g. excluding manual soldering,
- replacing them with more efficient ones – e.g. introducing wave soldering.
We have described these issues in detail in the article on DFM analysis>>
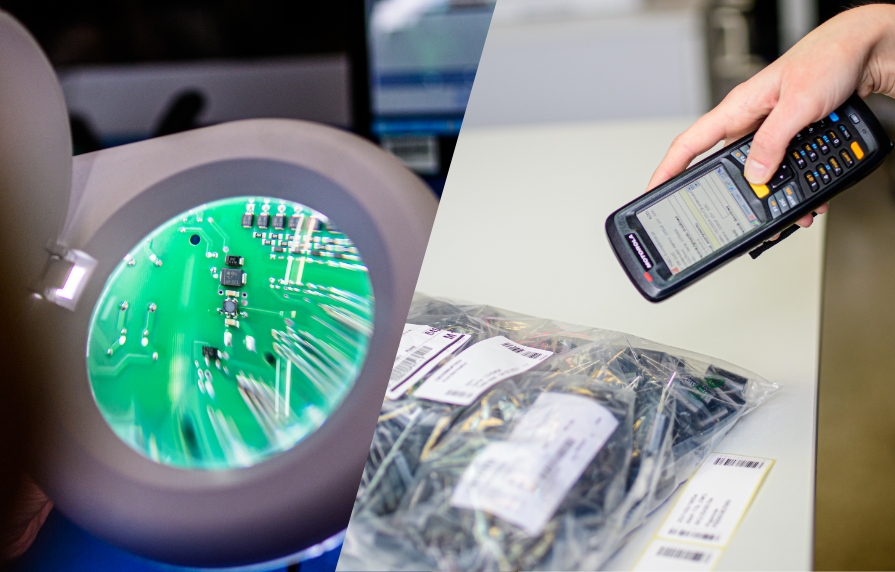
Experience in the industry tells us that approx. 3/4 of the costs are material costs. Optimisation of the BOM can have the best effect in the case of component groups with a particularly high proportion of the total costs.
A large proportion of the components listed on the BOM can often be replaced by cheaper substitutes in consultation with the team responsible for designing the device. Also, unavailable components can be replaced by equivalents or other components after a slight redesign.
We have been working in the electronic components industry for almost 35 years. Using our experience and direct contacts with suppliers, we assist customers in selecting more accessible and affordable replacements for BOM components. It is good practice to include in negotiations not only engineers, but also purchasing representatives who have up-to-date knowledge of fluctuations in the electronic components market.
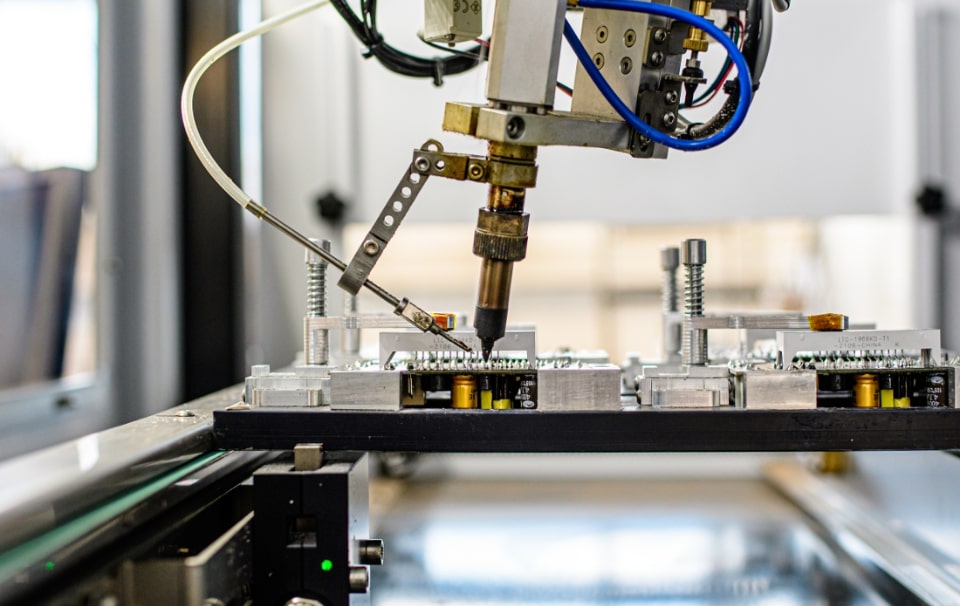
Through changes in the manufacturing process, labour efficiencies can be gained. The OEM’s engineers, in collaboration with the EMS partner’s engineers, should analyse the production process in depth and eliminate any bottlenecks that may affect project delays.
Depending on the type of project and scale of production, it should be considered whether it is better to work with a universal production line or whether it would be more beneficial to build a dedicated production line for the customer’s device series. Optimised set-ups, no changeovers, adjusting routes for optimum line timing reduces losses in the production process and therefore lowers the unit cost without any negative impact on quality. The work of experienced process engineers with operators makes it possible to spot activities or conditions that negatively affect labour intensity. Taking these suggestions into account provides the opportunity to make further savings in the process.

A very important aspect for avoiding additional costs is ensuring the quality of the PCBA. At JM elektronik, we carry out a number of activities in this area. In addition to a number of organisational solutions, procedures and analyses, we naturally apply advanced control of both the correctness of the assembly and often the correctness of the operation of the device. To this end, we have implemented the following procedures: Solder Paste Inspection (SPI), Automatic Optical Inspection 3D (AOI-3D), In-Circuit Testing (ICT) and functional testing.
The automation of production processes not only increases the accuracy of the inspection performed, but also means high reproducibility and significant savings in the time required to perform the inspection. The implementation of detailed procedures therefore allows short- and long-term savings, in the form of reduced time to market and a significant reduction in the risk of defects. We have extensive experience in building automatic functional testers. This procedure involves reproducing the duty cycle that the assembled board will perform in the final device and simulating the operation of the final device. Such a comprehensive test radically reduces the risk of defective products reaching the market.
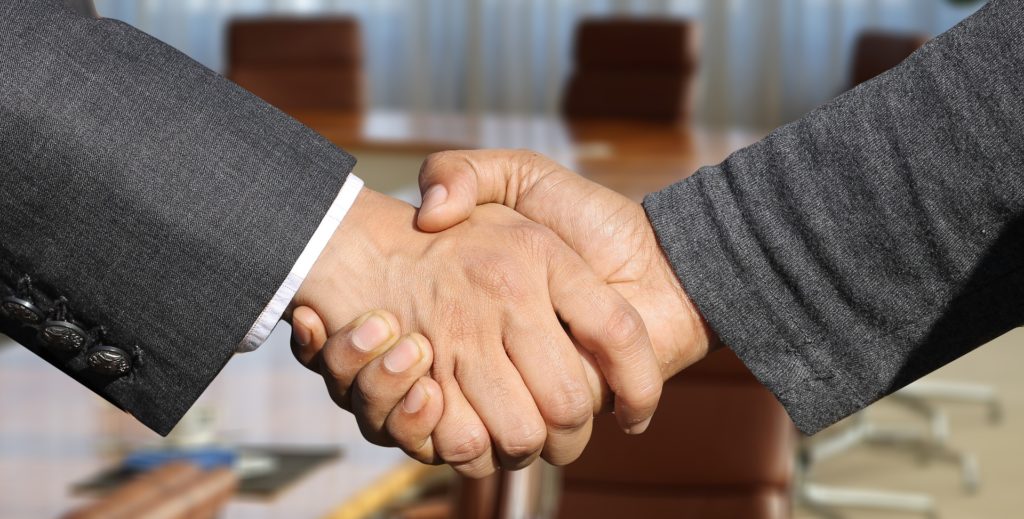
In all these areas, the basis for successful cost optimisation is good cooperation between the partners. The time spent on exchanging suggestions and experiences is always less costly than the time it takes to implement improvements or, in particular, to eliminate defects.
OEMs often set annual cost reduction targets, which they see as an opportunity to make their products more competitive. As a professional EMS partner, we will do our utmost to ensure that our customers spend their money wisely. Whenever possible, and even when it seems impossible, we will find new ways to increase efficiency and savings. We feel responsible for the product we supply to you, so not every way to cut costs is acceptable to us. Nevertheless, we always find methods that are safe for your brand.