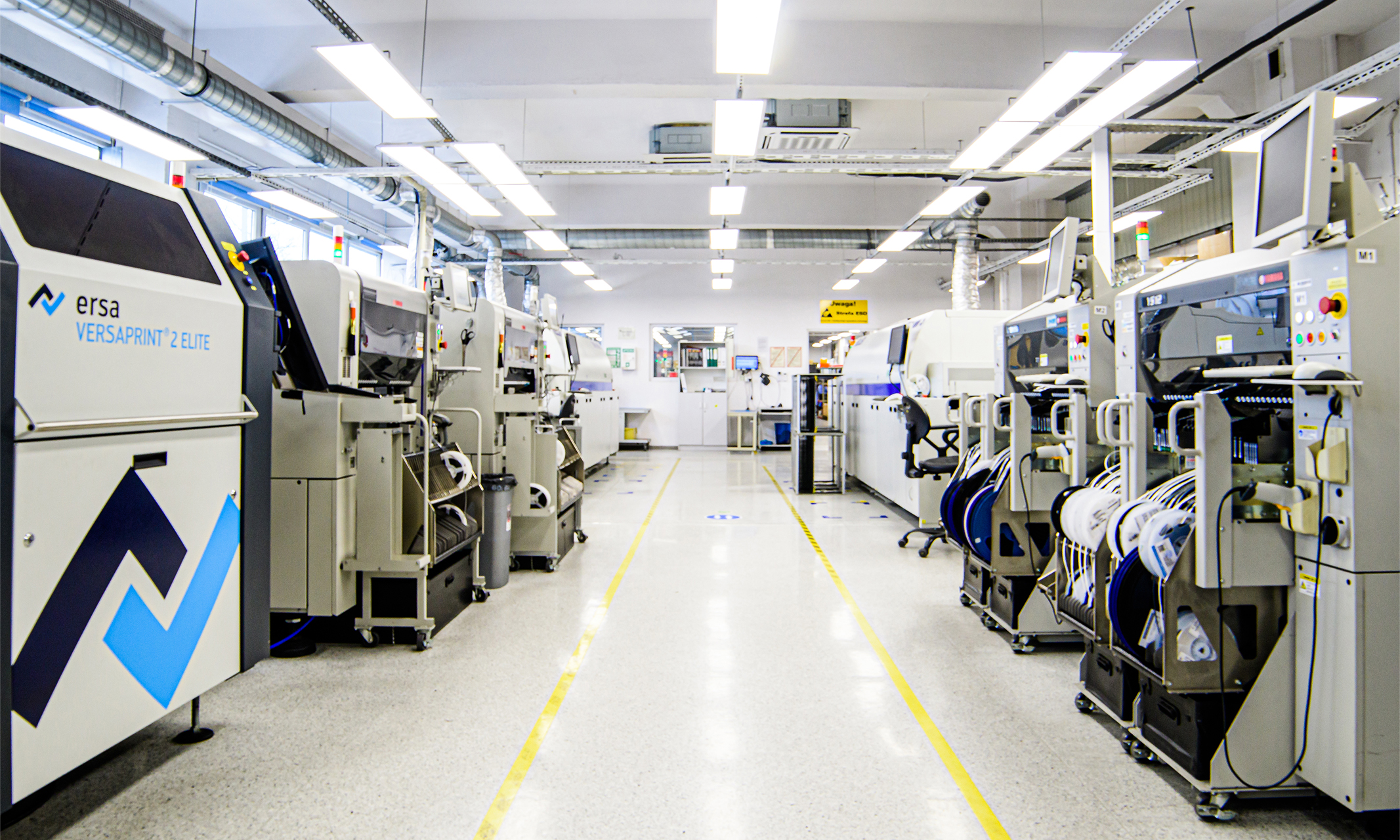
Component baking process significantly reduces the risk of PCBAs defects
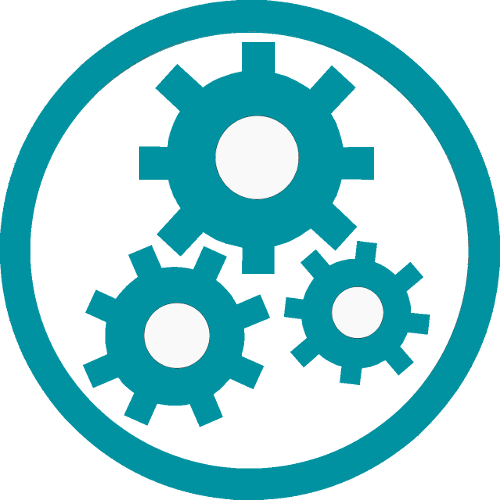
Can storing ICs or modules for just a few days without proper packaging increase the risk of defects in the products they will be used in?
Is it possible to resolve this?
What is the component baking process?
The increasing miniaturisation of electronics is placing ever greater demands on the quality of the materials used. Current technological processes are increasingly complex, requiring specialised, regularly updated knowledge and increasingly sophisticated equipment. Noteworthy is the fact that the appropriate quality of the assembled PCBA consists of many factors – proper parameters of the technological process, correct execution of assembly operations, ensuring safety against damage due to electrostatic discharge, proper packaging of products. The requirements concerning ensuring appropriate environmental parameters when storing electronic components are not always obvious.
Often underestimated, moisture requirements, the way components are packaged, are seen as less important. This is frequently due to the difficulty in detecting the root causes of some failures – their non-obviousness. It may also be the case when components are purchased from reliable suppliers, from current production lots, that problems resulting from improper storage do not become apparent for products manufactured immediately after component delivery.
However, it may turn out in the coming years that the scale of problems resulting from inadequate storage could increase rapidly.
In 2021/2022, due to the extreme difficulty in sourcing semiconductor components, many buyers opted to source ICs from completely unknown suppliers, often from production batches many years old. Forced to make such emergency deliveries, they had to lower requirements to ensure the availability of materials for future production.
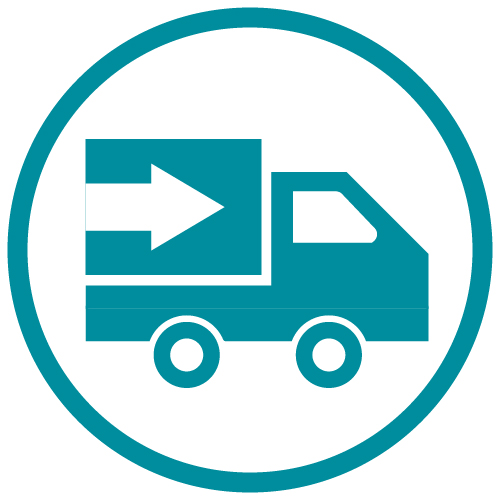
In 2023, when the availability problems ceased, it became apparent that supplies from regular purchasing sources had begun to arrive in bulk at customers’ warehouses and, as a result, many of the electronics manufacturers are facing excess inventory. According to the latest analysis, the value of excess inventory at contract manufacturers in Europe alone is in the billions of euros.
This means that inventory will be consumed for years, as well as being sold off on the open market and again exposed to uncontrolled storage conditions.
This situation represents an increased risk of assembly defects. These range from problems in the soldering process to defects whose root cause is moisture absorbed from the environment by the chip housings.
Electronic components mounted on a PCB are susceptible to varying degrees of moisture damage. Excess moisture, combined with a rapid rise of temperature during the soldering process, can cause defects in the component, such as micro-cracks, “popcorning” effect and delamination. Some of these become apparent during electrical testing or booting, and some of them result in increased failure only during use.
Component manufacturers determine the moisture sensitivity level (MSL – Moisture sensitivity level) of a component on a six-grade scale according to the J-STD- 020 standard.This standard specifies, among other things, how the component should be stored and the permissible time between removal of the component from the moisture barrier bag (MBB)and safe installation (assuming certain good environmental conditions of the environment). We distinguish between the following MSL classes:
- MSL 1 – lowest moisture sensitivity, can usually be exposed to ambient air without special precautions.
- MSL 2 – low sensitivity to moisture, can be exposed to ambient air, but after a year, ( and in the case of MSL 2a, just 4 weeks) should be subjected to an elemental annealing process.
- MSL 3 – moderate moisture sensitivity; minimise the amount of time components are exposed to ambient air, require more stringent storage procedures; should be subjected to component annealing after 168 hours (barely one week).
- MSL 4 – quite sensitive to moisture, requires careful handling and storage in a Moisture Barrier Bag (MBB); should be subjected to a component annealing process as early as 72 hours.
- MSL 5 – very moisture-sensitive, requires a rigorous approach and storage in a moisture barrier bag (MBB); after a specified time of 48 hours they should be subjected to a component annealing process.
- MSL 6 – extremely moisture-sensitive, must only be stored in a dry location, and heating of the component prior to installation is always required.
Precise information about a component’s sensitivity to moisture can be found on the caution label of properly packaged components. However, it is worth giving examples – the most popular microcontrollers are usually MSL3 grade, GSM/LTE communication modules often MSL4.
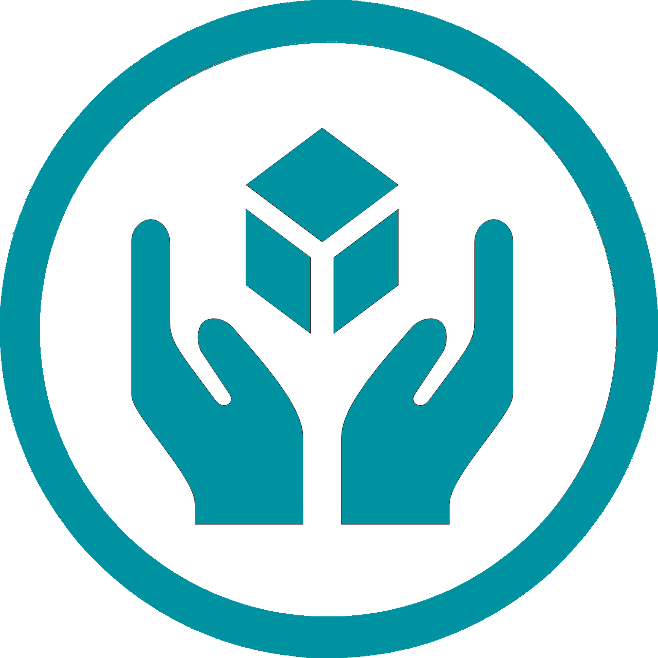
A component baking process is carried out to get rid of moisture from the case that was absorbed when stored without airtight vacuum packaging. The requirements for this process are contained in the relevant standard. The baking times vary from 5 hours to 67 days, depending on the class. Generally, the time is considerably shorter for higher temperatures, but this does not mean that higher drying temperatures should always be selected.
Immediately after this process, soldering is performed to almost completely eliminate potential defects caused by moisture.
In our business, we are often faced with the need to use components entrusted to us by customers who, however, are not always sure of the storage history of the purchased materials. In order to further increase our care for the final quality of the assembled devices, we purchased a laboratory dryer with forced air circulation that allows components to be heated over the full permissible temperature range. This is a state-of-the-art device equipped with, among other things, an event log, internal memory for measurement data and a multi-segment time-temperature profile.
The use of a pre-baking process allows us to eliminate the risk of damage resulting from not taking into account the destructive effect of moisture absorption in electronic components subjected to soldering processes.
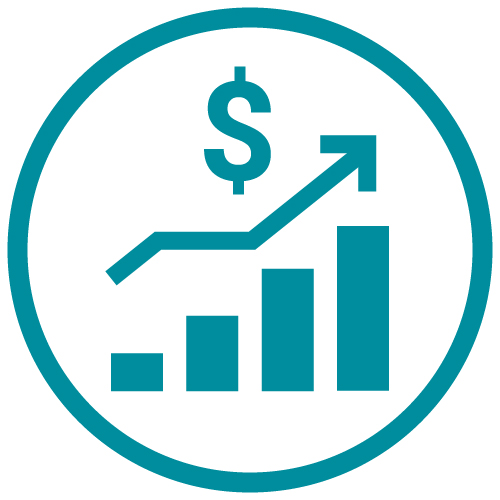