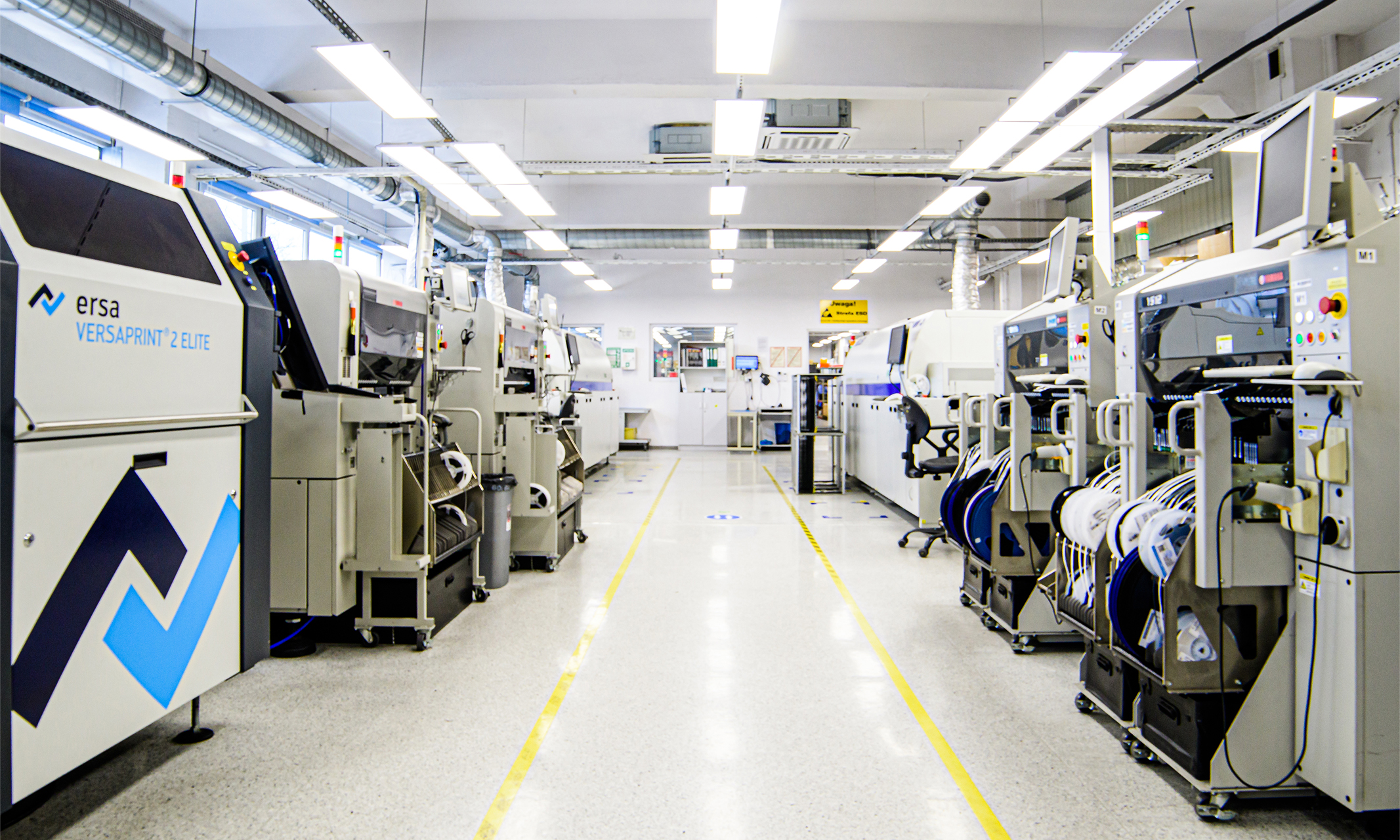
Wygrzewanie elementów znacznie zmniejsza ryzyko powstania wad wyrobów końcowych
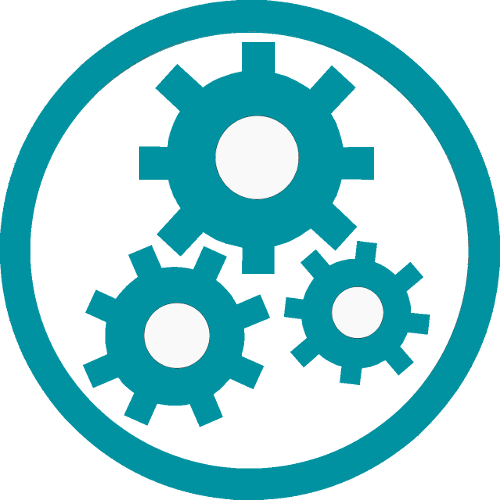
Czy przechowywanie układów scalonych lub modułów przez zaledwie kilka dni bez odpowiedniego opakowania może podnosić ryzyko wystąpienia wad wyrobów, w których będą zastosowane?
Czy da się to „odkręcić”?
Jakie znaczenie ma wygrzewanie elementów?
Postępująca miniaturyzacja elektroniki to coraz większe wymagania dotyczące jakości stosowanych materiałów. Obecne procesy technologiczne są coraz bardziej skomplikowane, wymagają specjalistycznej, regularnie aktualizowanej wiedzy oraz coraz bardziej zaawansowanego wyposażenia. Warto zwrócić uwagę, że na odpowiednią jakość zmontowanej PCBA składa się wiele czynników – odpowiednie parametry procesu technologicznego, poprawność wykonania operacji montażowych, zapewnienie bezpieczeństwa przed uszkodzeniami na skutek wyładowań elektrostatycznych, właściwy sposób pakowania wyrobów. Nie zawsze oczywiste są wymagania dotyczące zapewnienia odpowiednich parametrów środowiskowych podczas przechowywania elementów elektronicznych.
Często niedoceniane wymagania dotyczące wilgotności, sposobu pakowania komponentów są postrzegane jako mniej istotne. Wynika to na ogół z trudności w wykryciu przyczyn źródłowych niektórych uszkodzeń – ich nieoczywistość. Być może też z uwagi na zakupy komponentów realizowane u rzetelnych dostawców, z partii bieżącej produkcji problemy wynikające z niewłaściwego przechowywania nie ujawniają się dla wyrobów wyprodukowanych niezwłocznie po dostawie komponentów.
Jednak może się okazać w najbliższych latach, że skala problemów wynikających z niewłaściwego przechowywania może gwałtownie narastać.
W latach 2021/2022 z uwagi na niezwykłe trudności w pozyskaniu elementów półprzewodnikowych wielu kupców decydowało się na pozyskanie układów scalonych od zupełnie nieznanych dostawców, często z partii produkcyjnych sprzed wielu lat. Zmuszeni do dokonywania takich awaryjnych dostaw musieli obniżyć wymagania dla zapewnienia dostępności materiałów do przyszłej produkcji.
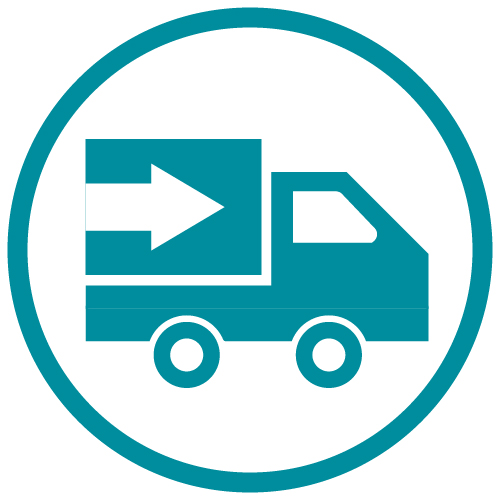
W roku 2023, kiedy problemy z dostępnością ustały okazało się, że dostawy z regularnych źródeł zakupowych zaczęły masowo docierać do magazynów Klientów i na skutek tego wielu z producentów urządzeń elektronicznych boryka się z nadmiernymi stanami magazynowymi. Według najnowszych analiz wartość nadmiernych zapasów u samych tylko producentów kontraktowych w Europie jest liczona w miliardach EUR.
To oznacza, że zapasy będą zużywane latami, a także upłynniane na wolnym rynku i ponownie narażone na przechowywanie w niekontrolowanych warunkach.
Taka sytuacja to podwyższone ryzyko występowania wad montażowych. Poczynając od problemów w procesie lutowania, a kończąc na uszkodzeniach, których przyczyną źródłowa jest wilgoć absorbowana z otoczenia przez obudowy układów scalonych.
Komponenty elektroniczne, montowane na płytce PCB są w różnym stopniu podatne na uszkodzenia spowodowane wilgocią. Jej nadmiar w połączeniu z gwałtownym wzrostem temperatury podczas procesu lutowania może spowodować defekty elementu, m.in., mikropęknięcia, „efekt popcorning’u”, delaminację. Część z nich ujawnia się przy próbie testowania elektrycznego czy uruchamiania, a część skutkuje zwiększoną awaryjnością dopiero podczas użytkowania.
Producenci komponentów określają poziom wrażliwości elementu na wilgoć (MSL – Moisture sensitivity level) w sześciostopniowej skali wg normy J-STD-020. Standard ten określa m.in. sposób przechowywania elementu oraz dopuszczalny czas pomiędzy wyjęciem komponentu z torby z barierą przeciwwilgociową (MBB) i bezpiecznym montażem (przy założeniu określonych dobrych warunków środowiskowych otoczenia). Wyróżniamy następujące klasy MSL:
- MLS 1 – najniższa wrażliwość na wilgoć, zwykle mogą być wystawione na działanie powietrza z otoczenia bez specjalnych środków ostrożności.
- MSL 2 – niska wrażliwość na wilgoć, mogą być wystawione na działanie powietrza z otoczenia, ale po upływie roku, (a w przypadku MSL 2a – zaledwie 4 tygodni) powinny być poddane procesowi wygrzewania elementów.
- MSL 3 – umiarkowana wrażliwość na wilgoć; należy zminimalizować czas, w którym komponenty są wystawione na działanie powietrza z otoczenia, wymagają bardziej rygorystycznych procedur przechowywania; po upływie 168 godzin (ledwie jeden tydzień) powinny być poddane procesowi wygrzewania elementów.
- MSL 4 – dość wrażliwe na wilgoć, wymagają ostrożnego obchodzenia się i przechowywania w torbie z barierą przeciwwilgociową (MBB); już po upływie 72 godzin powinny być poddane procesowi wygrzewania elementów.
- MSL 5 – bardzo wrażliwe na wilgoć, wymagają rygorystycznego podejścia i przechowywania w torbie z barierą przeciwwilgociową (MBB); po upływie określonego czasu 48 godzin powinny być poddane procesowi wygrzewania elementów.
- MSL 6 – wyjątkowo wrażliwe na wilgoć, muszą być przechowywane wyłącznie w suchych miejscach, zawsze wymagane jest wygrzewanie elementów przed montażem.
Precyzyjne informacje na temat wrażliwości komponentu na wilgoć znajdują się na etykiecie ostrzegawczej prawidłowo zapakowanych elementów. Warto jednak dać przykłady – najpopularniejsze mikrokontrolery mają zazwyczaj klasę MSL3, moduły komunikacji GSM/LTE często MSL4.
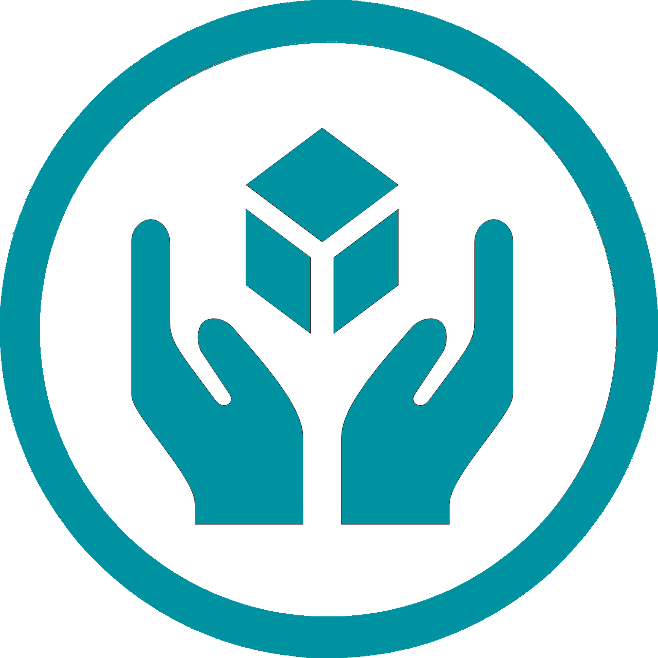
W celu pozbycia się wilgoci z obudowy, która została wchłonięta kiedy przechowywane były bez szczelnego, próżniowego opakowania realizowany jest proces wygrzewania wstępnego. Wymagania dotyczące jego przebiegu są zawarte w odpowiedniej normie. Czasy wygrzewania wahają się zależnie od klasy od 5 godzin do 67 dni. Generalnie dla wyższych temperatur czas ten jest wyraźnie krótszy, co jednak nie oznacza, że zawsze należy wybierać wyższe temperatury procesu suszenia.
Bezpośrednio po tym procesie wykonywane jest lutowanie, aby w ten sposób niemal całkowicie wyeliminować potencjalne defekty spowodowane wilgocią.
W naszej działalności często spotykamy się z koniecznością użycia komponentów powierzonych przez Klientów, którzy jednak nie zawsze są pewni historii przechowywania zakupionych materiałów. Dla dalszego zwiększenia dbałości o finalną jakość zmontowanych urządzeń zakupiliśmy suszarkę laboratoryjną z wymuszonym obiegiem powietrza umożliwiającą wygrzewanie elementów w pełnym dopuszczalnym zakresie temperaturowym. Jest to urządzenie najnowszej generacji, wyposażone m.in. w rejestr zdarzeń, pamięć wewnętrzną dla danych pomiarowych czy wielosegmentowy profil czasowo-temperaturowy.
Zastosowanie procesu wstępnego wygrzewania pozwala nam eliminować ryzyko uszkodzeń wynikających z nieuwzględnienia niszczącego wpływu absorbcji wilgoci w elementy elektroniczne poddawane procesom lutowania.
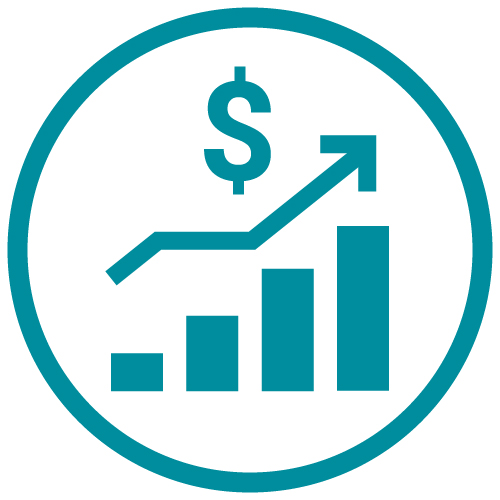