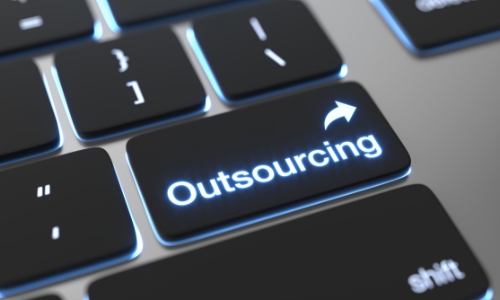
Electronics manufacturing outsourcing as a recipe for staff shortages in the labour market?
Electronics manufacturing outsourcing is becoming an attractive option for OEMs when dealing with skills shortages in the labour market. This solution can bring numerous benefits, significant cost reductions, resilience to market fluctuations and optimisation of the business model.
The labour market in manufacturing is constantly suffering from a lack of available resources. In particular, professionals and skilled workers are the problem. This creates a serious gap and often a very tangible financial loss.
Many OEMs (original equipment manufacturers) with production facilities are now looking to hire, but are struggling to find suitable employees.
In addition, the fierce competition for talent and soaring wages mean that many companies are unable to retain suitably skilled employees because often their workload and the challenges they are being asked to face are not great enough.
So, if you are looking at the skills shortage and seeing its daily impact on your productivity and ability to compete there will come a point when you will consider electronics manufacturing outsourcing as a way to address such challenges.
It is questionable whether outsourcing partners (such as contract manufacturing EMS providers) will be free of such problems when they operate in the same labour market. Undoubtedly, they are also affected by similar difficulties, but because of their focus on their area of expertise, they can ensure that they have multi-member teams, whose members are delegated to different projects and exchange, substitute, transfer knowledge, gain experience all the time. The situation is different in companies for which electronics production is only a part of the business. It is often difficult to have a large team of specialists there because there are simply not enough tasks for them.
When the situation becomes difficult for companies carrying out production processes on their own with limited facilities and the ability to scale, EMS companies have much greater options.
More informations about electronics manufacturing outsourcing>>
Recruitment in the current labour market is difficult. Companies have to put in extra effort to attract candidates, and those that are successful often have to allocate high amounts of money in advertising budgets making talent acquisition totals very high. This is especially true for highly specialised positions.
Alternatively, working with recruitment agencies is an effective way of hiring candidates, but it is also an expensive option. Specialised services provided by agencies come at a premium because the quality of candidates put forward is expected to be higher in order to reduce time, although there is still no guarantee that the ideal candidate will be brought forward.
Whichever hiring method you choose, the costs will be higher than if you outsource the same task. Especially as it will require a commitment to interviews, selection, meetings – these processes often stretch out over months.
And once you’ve found and hired the right candidate, you’ll still incur costs for staff induction and training. Again, this process is costly and senior members of staff have to spend their time developing new employees. The high proportion of new staff who leave within the first few months often means that high costs can go to waste.
Electronics manufacturing outsourcing can significantly reduce, if not eliminate, these expenses.
We realise that in recent years companies have constantly had to offer more extra benefits in order to attract and retain employees. Private medical care, additional life insurance, psychological care, fruit Thursdays, recreation zones in workplaces. These are already an everyday occurrence and an additional cost. And let’s not forget the costs necessary for the professional development of these employees.
EMS companies may have to offer many similar bonuses, but with the right scale of operation, the unit cost per man-hour of work is significantly lower.
The need to adapt the scale of production to the market is, of course, essential. We have all felt in recent years that the ability to respond flexibly and efficiently to both decelerating and surging demand has determined the success of entire projects and businesses.
OEMs who want to scale their business need many people with a range of technical skills. However, hiring staff with every necessary skill is an inefficient use of resources and probably not economically feasible.
Electronics manufacturing outsourcing allows permanent access to a much larger talent pool. This allows OEMs to be much more flexible in the use of their resources. EMS companies’ business models are flexible, so working with one allows them to adapt to anticipated and unforeseen situations.
For example, it is much easier to respond to a sudden increase in demand if you have an EMS partner. Economies of scale also mean that it will cost less than if you try to scale in-house.
Every OEM wants to sell more equipment but when demand increases there are many issues to be resolved – staffing, training, maintaining quality, premises constraints, availability of working and investment capital.
This is where the real problems begin, as OEMs can easily fall into one of two traps: either it is impossible to meet customer demand or the quality of service falls. Both of these situations can seriously affect customer satisfaction and damage their reputation in the long term.
EMS providers are set up to manage spikes in demand. Due to the mix of customers and market sectors, EMS companies are more flexible and better able to manage the flexibility of their capacity. Shared inventories for all customers ensure easier availability of materials, and their investment in state-of-the-art technology allows them to scale easily without additional costs for OEM customers.
Electronics manufacturing is increasingly demanding high levels of expertise. The challenges for process engineers or quality engineers are very high and therefore the costs of acquiring and maintaining such resources are very high. Often unreasonable. It is much more important to ensure that you have the best competence in the areas that allow your company to be unique and win in the competition.
Most experienced OEMs outsource at least part of their production. They have found that the benefits radically outweigh any possible concerns. The difficult labour market indicates even more clearly that further outsourcing of even more processes is a solution to problems that were not there in the days of easy availability of employees.