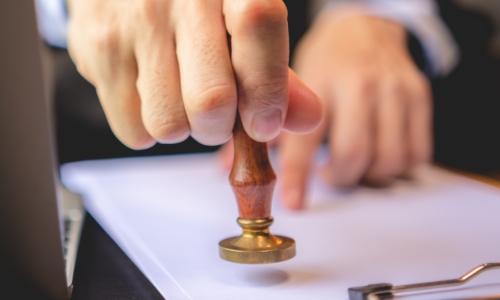

Printed Circuit Board Assembly (PCBA)
Our offer is addressed to companies offering electronic devices or products containing electronic assemblies, which want to focus on the most important areas of their business, rather than on routine processes.
We are happy to provide outsourcing of all production related tasks.
We usually handle production in batches of 500 – 10,000 units. We specialise in medium and highly complex products. But we also produce simpler ones.
Each customer can count on an individual approach aimed at the best possible understanding of the customer’s needs and setting up a suitable offer.
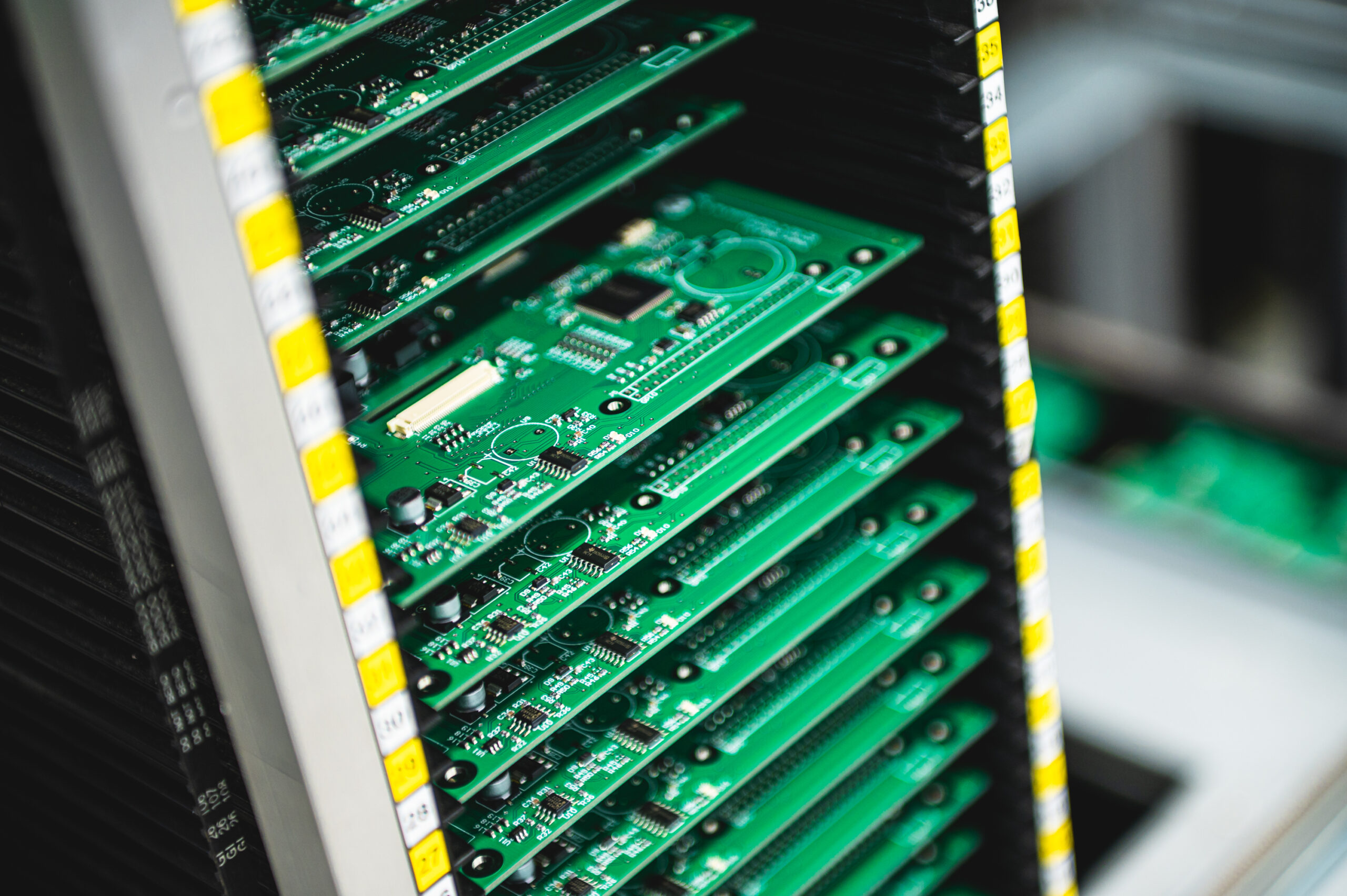
Surface Mount Technology (SMT)
We handle large production batches as well as smaller quantities of complex products. We are able to mount very complex boards containing up to 300 DIFFERENT SMD components. We assemble SMD components in accordance with generally applicable standards, with attention to details at every stage.
We have years of practice assembling BGA, MLF, Fine Pitch, passive components in sizes from 0201, as well as hybrid modules (GSM, GPS, WiFi, Bluetooth and other devices). We work on printed circuit boards made of various materials. We are able to carry out assembly on laminate down to 0.3 mm thickness.
Our customers benefit from fully automated new SMT assembly lines equipped Yamaha Pick&Place machines, with a total capacity of 110,000 parts per hour.
This equipment allows for double-sided assembly of components.
The paste application process is controlled by an automated SPI.
Full redundancy of resources – equipping the lines with the same ovens, P&P machines, and stencil printers – allows for optimized allocation of orders between the lines, and provides additional advantage in the production continuity management process.
The production process on SMT lines is further accompanied by automated AOI-3D control.
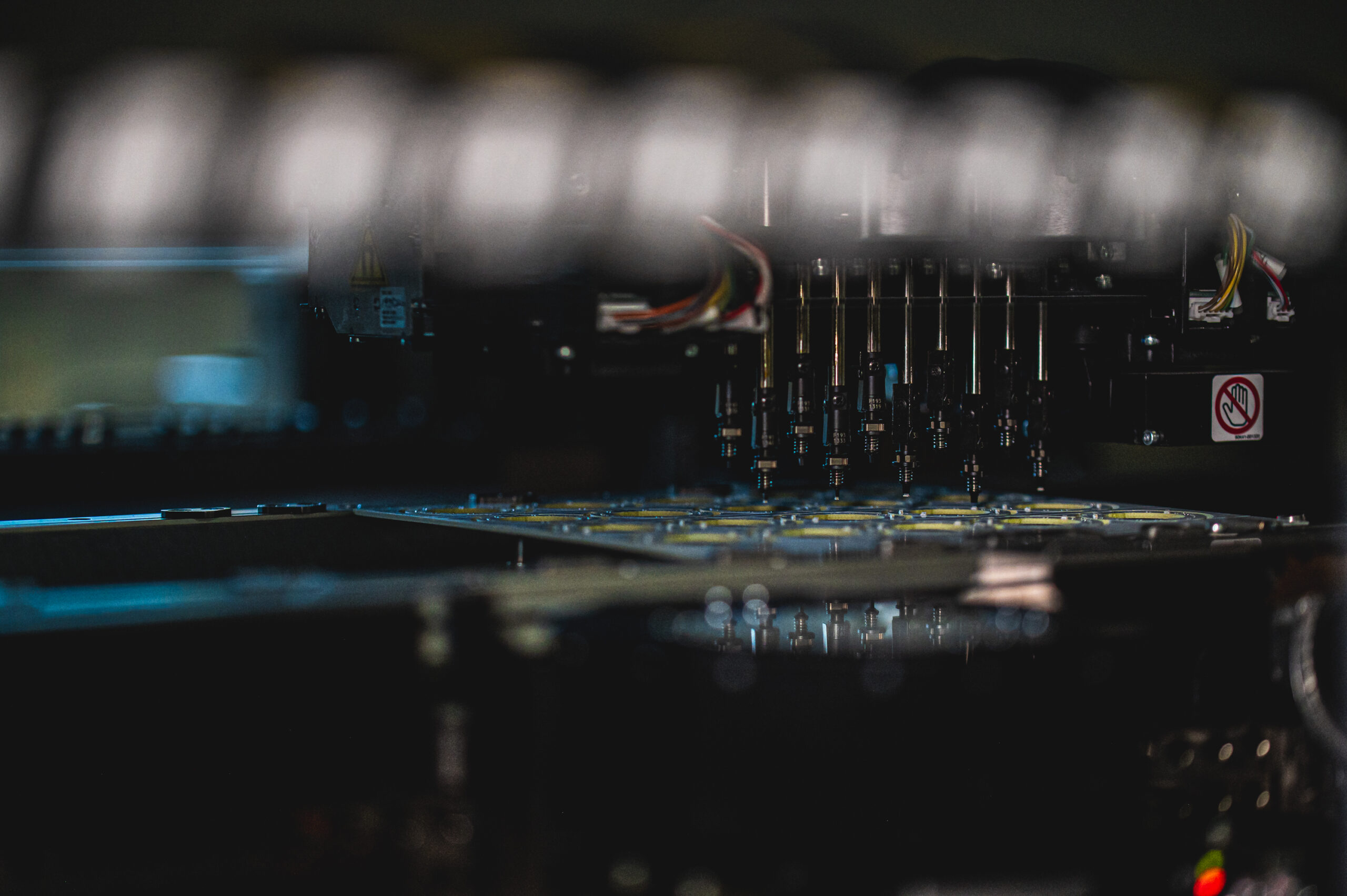
Through Hole Technology (THT)
As far as THT technology assembly is concerned, we offer our customers following options:
- 3 wave soldering assembly lines;
- Selective soldering in a protective atmosphere;
- THT soldering robot;
- Automated assembly of through-hole type components;
- Manual assembly and soldering.
In automated soldering process we use advanced tools to achieve excellent quality connections and high cleanness of boards.
Our experience in mixed technology PCB assembly, where some part of the assembly is carried out in THT technology using wave, and some is carried out in surface mount technology, sets us apart. We support customers preparing production tools, in particular fixtures and maskings that enable the production of such mixed boards.
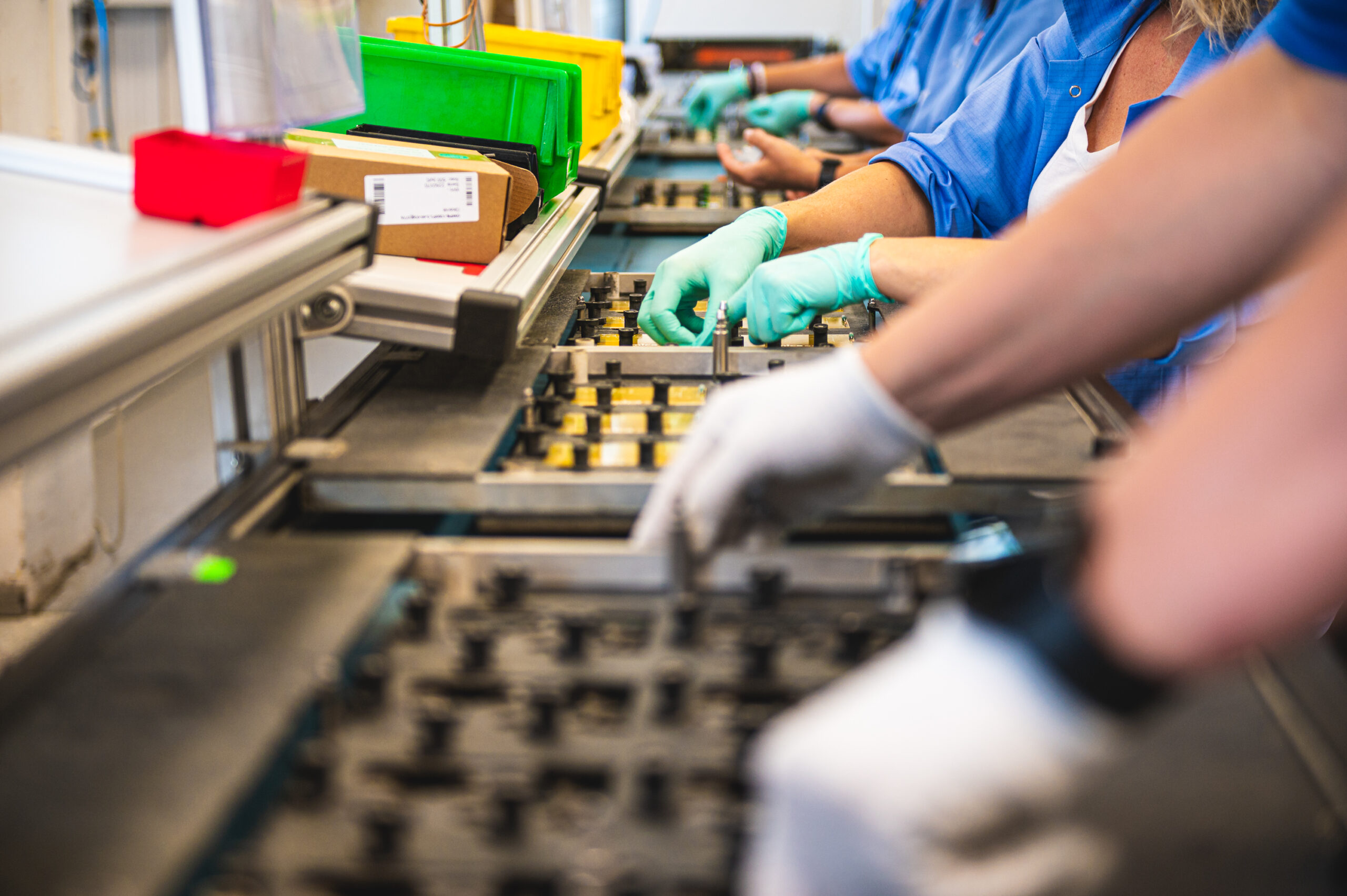
Manual assembly with manual soldering
A team of over 70 experienced assembly personnel, who are skilled in reading documentation and carrying out assembly in line with accepted good practice, work to fulfill the orders placed by our customers.
Highly experienced staff act as leaders, taking care of repeatability and high quality of the process.
The assembly stations, where manual assembly takes place, provide a good level of ESD protection, are equipped with professional soldering tools, lighting, fume hoods and barcode/2D scanners with terminals providing access to the MES (IT production management system), which ensures traceability for components and products.
We usually work two shifts, six days a week.
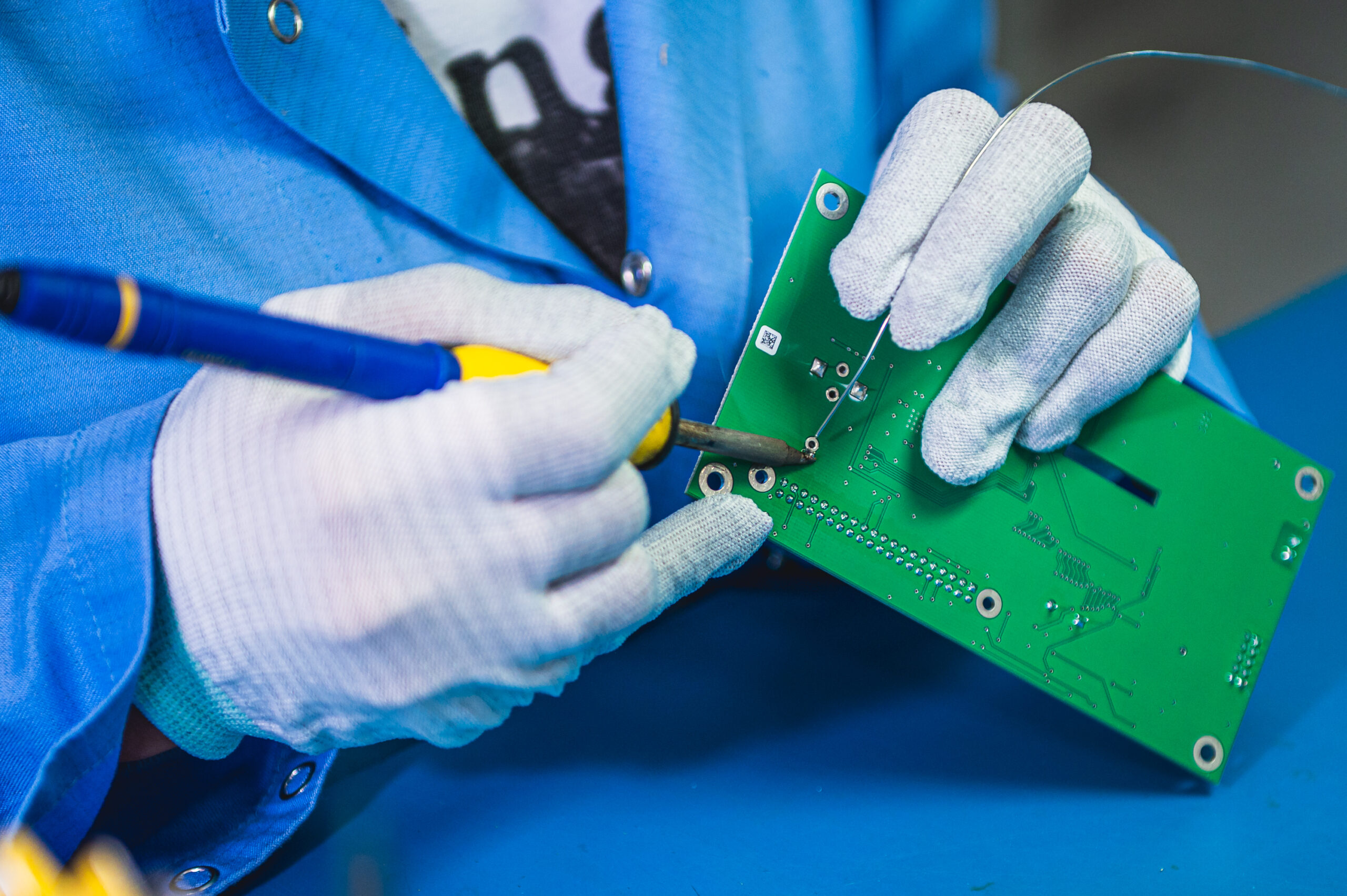
Selective soldering in a protective gas atmosphere
Our selective wave soldering line is equipped with two soldering modules – two separate pumps with nozzles immersed in one pot. Selective wave soldering takes place in a nitrogen protective atmosphere – this significantly improves the quality of connections.
A substantial advantage of selective wave soldering is the possibility to speed up the process of producing the first products by weeks. The use of laminar line soldering pallets requires their prior development for a specific product, ordering, production and testing, which takes valuable time.
A second argument for using a selective soldering machine is the lower initial production cost for smaller batches or when introducing a new product. This is because you have to pay for pallets even if the first batch of products is short and there is no guarantee that it will be repeated.
The use of selective soldering lines enables components to be intermixed – there is little temperature influence from the nozzles – which opens up new design perspectives for customers.
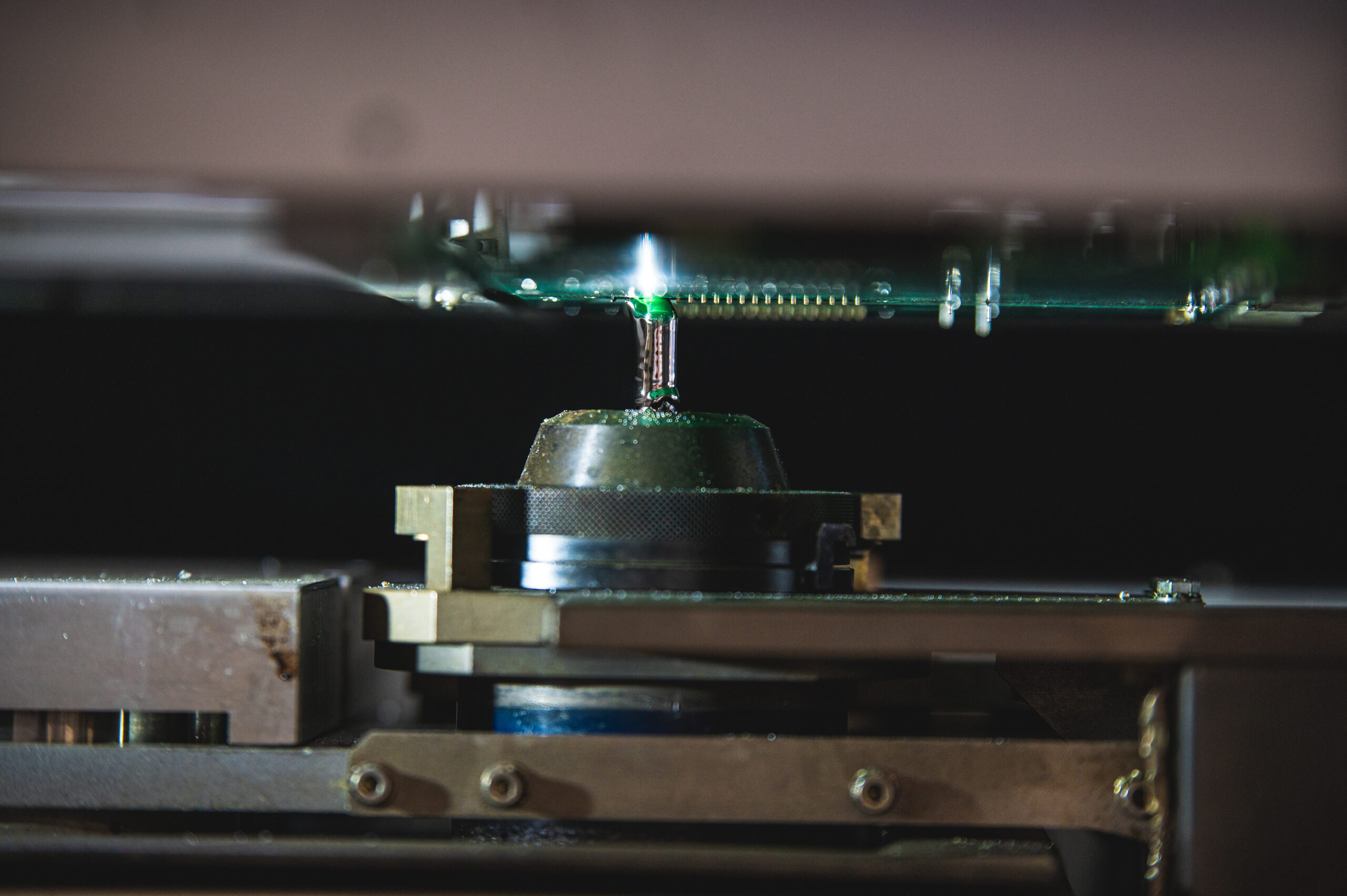
Soldering robot
We have the competences and machinery enabling us to carry out the soldering process with the use of a soldering robot, which is increasingly becoming an alternative to manual assembly, due to full repeatability of the soldering process and its automation.
Our engineers independently develop the necessary tools and accessories and define the complete process in technological terms, including the robot programming.
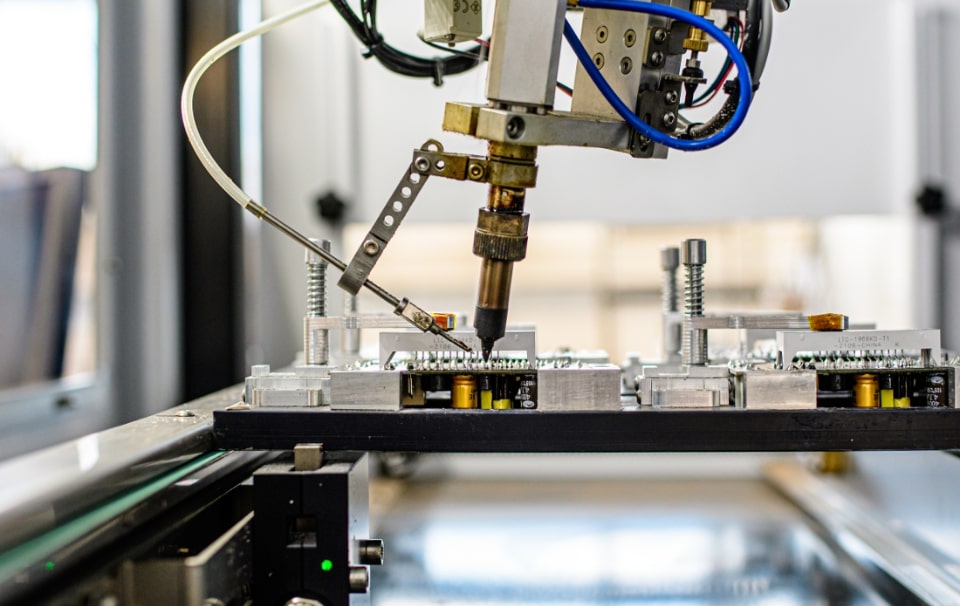
Chemical processes
As part of our assembly processes, we are constantly developing gluing, conformal coating and potting processes. The processes are used to protect electronic devices from negative environmental influences, from unauthorised access or simply in mechanical assembly processes. Thanks to our experience and appropriate equipment, we implement methods adapted to the requirements of a given application, configure them and control them automatically. In gluing processes, we use robotic stations and dedicated tools and jigs developed by our team of process engineers.
We have extensive experience in conformal coating of printed circuit boards using various technologies. Hundreds of thousands of coated boards processed on our selective coating lines and dip coating lines have allowed us to gain know-how and expertise in this field.
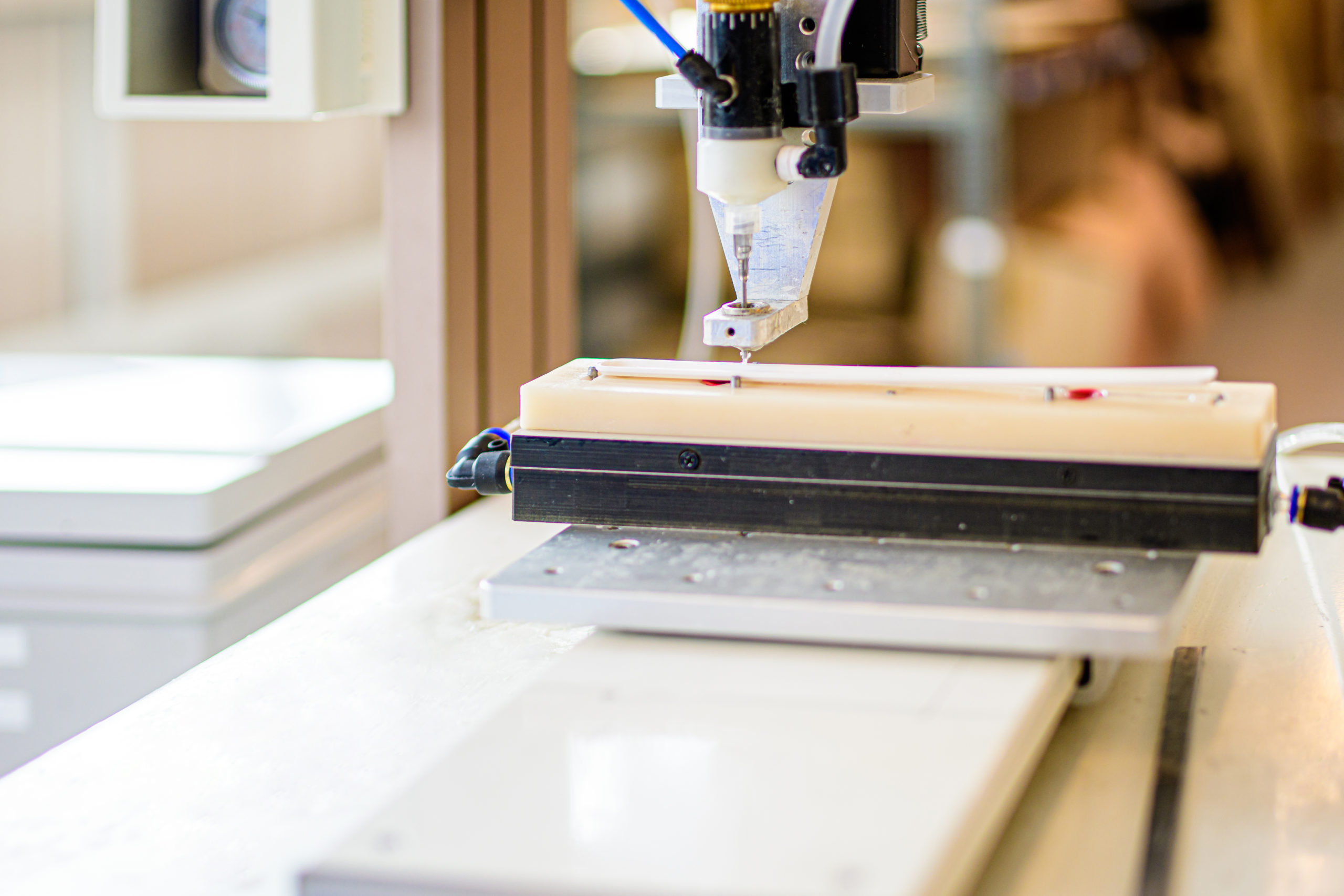
Tools making
When developing optimum assembly processes, we often use dedicated jigs and tools to achieve exceptional productivity, error-free assembly, and ergonomics. We have our own machinery and skilled in-house design engineers who develop the necessary tools, jigs and fixtures.
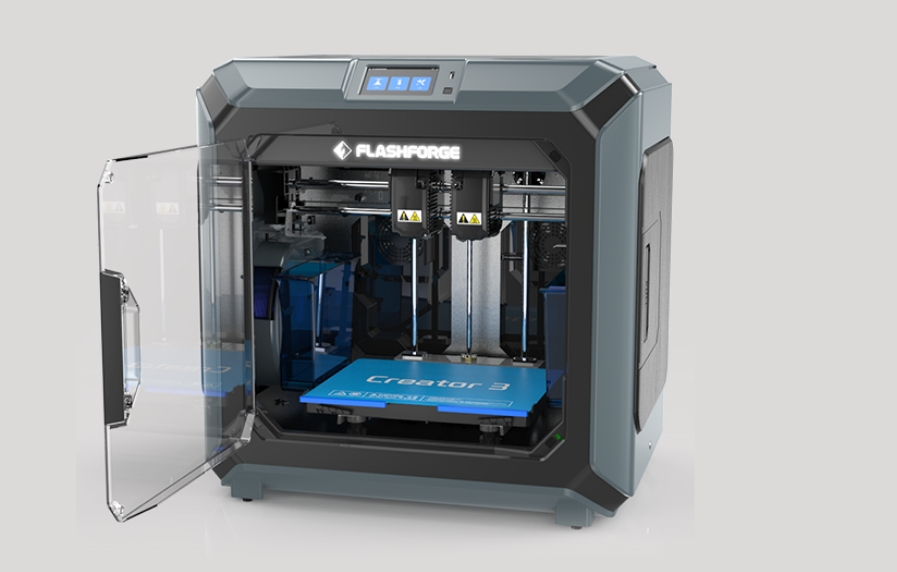