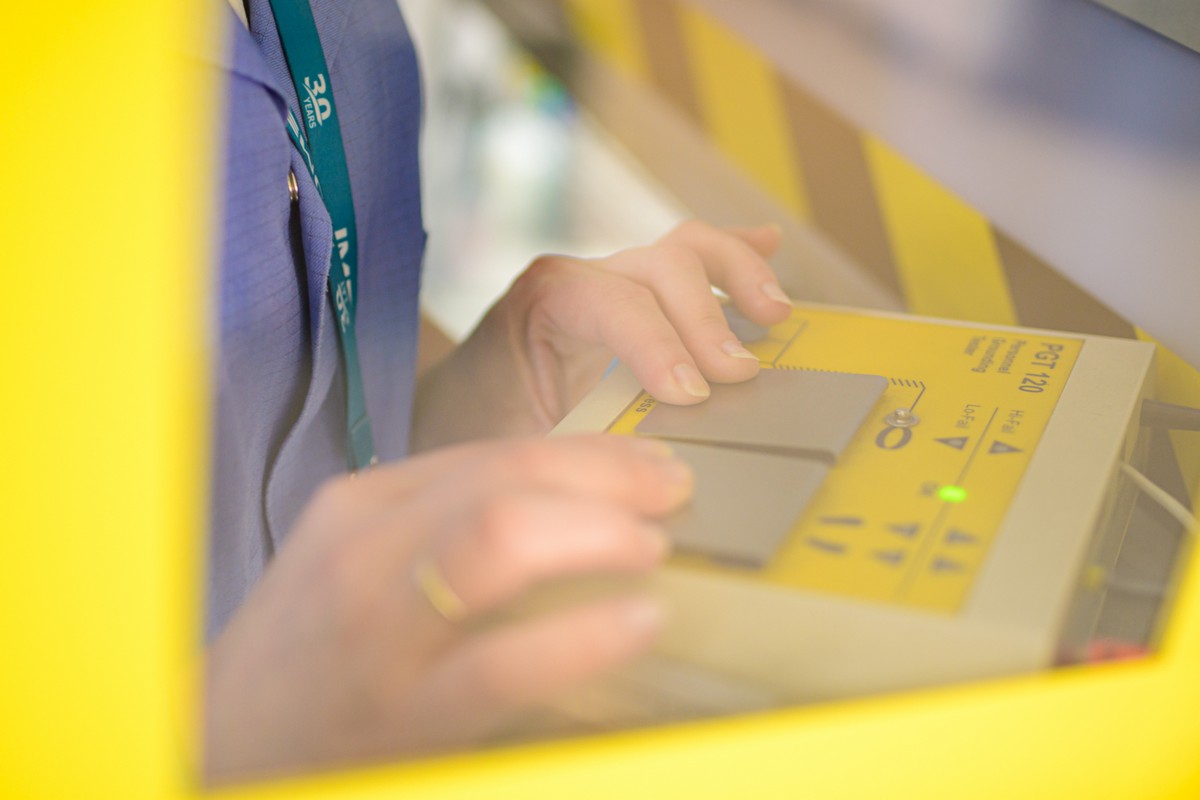
Electrostatic discharges are a serious challenge for electronics manufacturers. How do we prevent them?
ESD (ElectroStatic Discharge) are with us everywhere. What risks can they pose to electronic devices?
Can a discharge that is not perceptible to humans damage a device?
How do we prevent this?
Electrostatic discharge (ESD) is the sudden flow of static electricity from one object to another, due to different potentials passing from electrostatic sources. When electrical energy has the possibility of coming into contact with or even close to a sensitive component, it can cause damage.
This is a very common phenomenon, also surrounding us in everyday life. A popular example of a very strong electrostatic discharge is lightning during a thunderstorm.
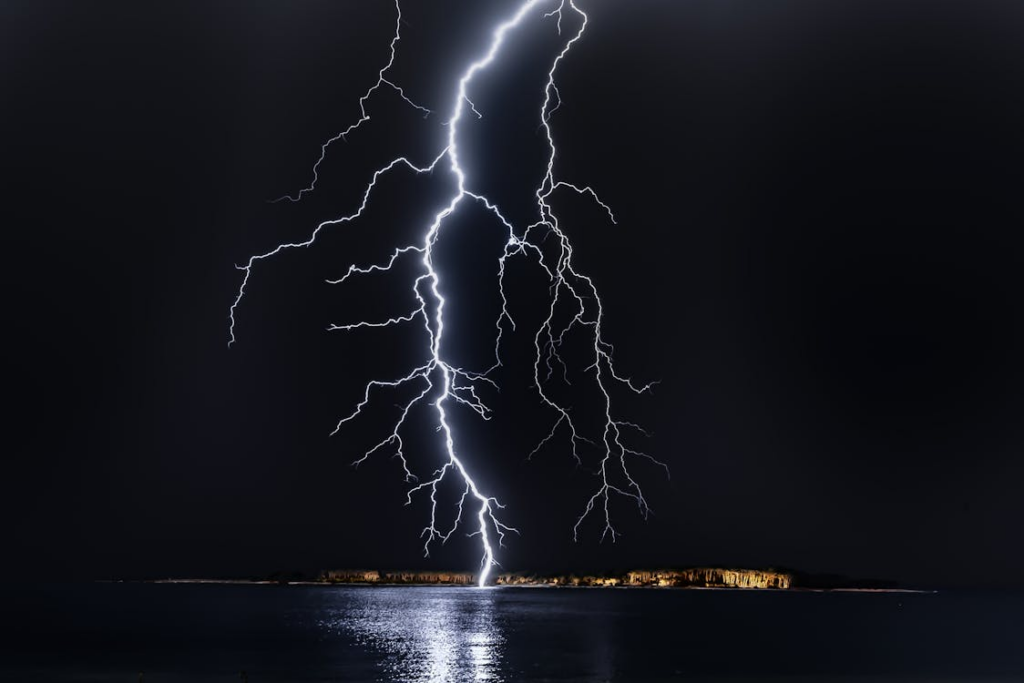
We know that lightning is a great danger to our home/office appliances – the sudden increase in voltage in the electrical system leads to their damage. Unfortunately, any discharge, even one that is invisible to humans, carries a risk for electrical equipment, especially for components that are particularly ESD-sensitive. For this reason, it is extremely important for a professional electronics supplier to protect devices and components against discharges. As a result, customers do not have to fear that their product will contain defects.
Electrostatic discharge usually occurs when objects or materials with different electrostatic potentials come into contact with each other, for example when materials rub against each other or become separated. As a result of the contact, one of the materials assumes a positive charge and the other becomes negatively charged. As a result, the material acquires an electrostatic charge, which is transferred on contact with the conductor – and so a discharge occurs.
A list of materials in terms of polarity and magnitude of charge is called a triboelectric series. During the discharge, materials that are classified in the positive range of the series transfer electrons to materials classified in the negative range, and materials that are classified in the negative range of the series transfer electrons to materials classified in the positive range. The prevalence of discharge is a challenge for electronics manufacturers. Discharge-causing contact between materials can occur even during such prosaic activities as walking, as soles rubbing against the floor can create an electrostatic charge. It is easy to see that every step can potentially cause ESD. On top of this, shoes or clothing can amplify this effect, so specialised clothing is required.
Damage to electronic components can occur in a number of ways: through contact between the component and an electrified component, contact between the component and humans, or even during the automatic transport of equipment. Almost the entire environment is involved: from temperature and humidity to the type of surface on which the component is stored or transported.
The miniaturisation of devices has increased their sensitivity to discharge. The almost microscopic size of the network of paths and structures in some components means that even a relatively low voltage can permanently damage the component. For example, for a person to notice a discharge, it should be around 3,500 volts. An integrated circuit can damage even a voltage of 10 V. Meanwhile, a walk can produce a voltage of around 1500 V. It is not only voltage that has a detrimental effect on equipment. Very high temperatures are also generated during ESD. When the discharge reaches a sensitive electronic component: semiconductor, expansion card and others, due to the rise in temperature, joints can melt or vapurise, causing failure.
The defects that arise can be visible immediately. A test or even a person with the naked eye can detect that a circuit is burnt out or melted. Much more problematic are hidden defects, which usually arise at lower voltages. The discharge does not necessarily damage the product completely, but may weaken individual components of the device, such as contacts or insulation. It is possible that the defect will not be detected either during the manufacturing process or during typical use of the device. Only prolonged intensive use can amplify the defect to such an extent that the device ceases to function properly and a slightly damaged contact wears out more quickly. ESD will initiate a process that can lead to malfunctioning of the device or a shortened lifespan.
Discharge occurs as a result of a potential difference, which is why workstations should be equipped with an earthing (grounding) system. Ensuring the correct level of surface resistance, i.e. the effective discharge of charges to ground (whether from the operator, machinery, tools or even shop equipment) will result in a continuous equilibration of potentials so that ESD does not occur.
Of course, this appropriate level of surface resistance, but also other parameters, are detailed in standards. We work on the basis of the recognised IPC-A-610 standard, which we strictly adhere to, meeting the standardisation requirements for electronics assembly and production. The implementation of the standards is supervised by certified IPC trainers.
Protection against electrostatic discharge is also defined by a number of other standards. General conditions are dealt with by the standards: PN-E-05204:1994, PN-EN 61340-5-1:2017-01, PN-EN 61340-2-1:2015-12; on flooring and footwear: PN-EN IEC 61340-4-5:2018-09, PN-EN IEC 61340-4-3:2018-04, PN-EN 61340-4-1:2006; on clothing and armbands: PN-EN 61340-4-9:2016-11, PN-EN 61340-4-6:2015-11.
It is worth noting that the system of standards places particular emphasis on four aspects: flooring, footwear, clothing and banding. The floor – because enabling walking or transport friction causes electrification, as mentioned earlier. Therefore, the floor should have antistatic properties and the ability to dissipate and ground charges.
Specialist ESD footwear is that which has an electrical resistance of between 0.75 MΩ and 35 MΩ and has the properties to dissipate charges from our body to ground.
ESD clothing is designed to counteract the electrification that occurs during human movement when the various garments rub against each other. Specialised clothing also has dissipative properties to provide adequate protection against discharges.
Discharge created by touching is counteracted by a wrist band. It consists of a metal applied directly to the fitter’s skin and a grounding wire. In this way, the charges accumulated on the skin or clothing are directly discharged to ground, so that also the electrical potential of the worker’s body is almost equal to the ground potential. This relatively simple solution offers the highest guarantee of protection against ESD.
At JM elektronik, we apply these principles rigorously. All our employees are properly trained. We do not allow the customer to receive faulty equipment.
An Electrostatic Protected Area (EPA) is a designated and marked protected area in which ESD standards are strictly adhered to. In this area, all ESD-sensitive surfaces, objects, people and equipment are kept at the same electrical potential. In our company, the zone covers the entire production area.
Working with customers also means sharing responsibility for the equipment produced. We ensure the highest standards of ESD protection so that our customers, and their end customers, are confident that they have a defect-free product. Choosing a professional EMS partner ensures that the lifespan of the end products is adequate, so that customers are not discouraged by the brand.